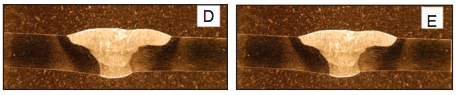
02 Sep L’importance du gaz d’inertage sur les propriétés des soudures TIG de l’inox 304H
L’importance du gaz d’inertage sur les propriétés des soudures TIG de l’inox 304H
par E. TABAN, E. KALUC et T. S. AYKAN
Des essais ont permis de mettre en évidence les effets de différents gaz d’inertage sur la microstructure, la résistance à la corrosion , à la rupture, à la déformation, aux impacts de l’acier inox 304H après soudage .
Paramètres du soudage
Le soudage à l’arc tungstène a été utilisé pour la passe de fond et la deuxième passe sur le pipe en 304H, avec de l’argon comme gaz de protection .
Le joint soudé marqué 04H NP (no purge/sans inertage ) a été réalisé sans aucun inertage lors de la passe de fond. Les joints suivants ont été réalisés sous inertage avec de l’argon pur, de l’azote pur, un mélange Ar+5%N2, et un mélange N2+10%H2, respectivement, sur la passe de fond. Outre la passe de fond, cinq passes supplémentaires ont été réalisées pour terminer les soudures.
Les pipes soudés sont appelés respectivement 04H A (inertage à l’argon), 04H N (azote), 04H AN (Ar+N2), 04H NH (N2+H2). Durant toute la phase de soudage , l’inertage a été maintenu jusqu’au refroidissement de la racine et de toutes les passes. Des baguettes TIG ER 308H ont été utilisées comme métal d’apport. La composition chimique du métal d’apport est donnée dans le Tableau 2.
La taille de l’ouverture de la racine a été maintenue en faisant quelques points de soudure avant le soudage proprement dit. On a lancé le soudage une fois le taux d’oxygène de 10 ppm atteint, vérifié par un mesureur approprié. Les détails de la procédure desoudage sont indiqués Tableau 3.
Des coupes transversales prélevées sur les cordons de soudure ont été préparées selon les techniques métallographiques standard : meulage sur des disques en composite, puis polissage sur des plateaux textiles avec des suspensions de diamant de tailles de grains de plus en plus fines.
Les échantillons ont été attaqués en condition électrolytique dans de l’acide oxalique, pour évaluation de la microstructure. En outre, un deuxième ensemble d’échantillons a été préparé et soumis à un réactif d’attaque colorée en solution de Lichtenegger, afin de déterminer le mode de solidification.
Le taux de ferrite de la première passe et de la passe finale, ainsi que celui du métal de base, ont été mesurés avec un Ferritscope®, en faisant la mesure à la surface de la première passe. On a fait la mesure en au moins 15 points sur chaque échantillon, afin de déterminer la teneur en ferrite (indiqué comme le Ferrite Number, ou FN).
La composition chimique des joints a été atteinte par la Spectrométrie à Décharge Luminescente (SDL ; GDOES, en anglais). Par ailleurs, un équipement de combustion Leco a été utilisé pour connaître les taux de N2, 02 et H2 de la racine.
Les valeurs Vickers ont été déterminées avec une charge de 10 kg sur une machine de dureté Instron sur la coupe transversale de chaque soudure , selon les pratiques définies dans les normes européennes (EN standards). Trois mesures ont été effectuées sur la surface pour le métal de la racine (≤ 2 mm de profondeur depuis la surface de la racine) et pour le métal de base.
Des essais de corrosion intergranulaire et de corrosion par piqûre selon les normes EN3157/EN ISO 3651-2 et ASTM G48, respectivement.
L’essai de corrosion intergranulaire a été mené par immersion dans une solution bouillante d’acide sulfurique-sulfate de cuivrependant 20 heures, puis par flexion des échantillons.
Les échantillons pour la corrosion par piqûre ont été conservés 72 heures dans une solution de chlorure ferrique à 50°C. On a mesuré les pertes de poids. On a fait des photomacrographies des échantillons pour les échantillons soumis à la corrosionintergranulaire aussi bien que pour ceux soumis à la corrosion par piqûre .
Des échantillons de tous les joints soudés ont été préparés pour la mesure de la résistance à la rupture transversale, selon lanorme API 1104, puis soumis à essai à température ambiante sur une machine hydraulique.
Fig. 1 :
Fig. 1 — Photographies montrant la racine des joints soudés sur des pipes en acier inox 304H, après la première passé et les cinq passes ultérieures.A — 04H NPB — 04H AC —04H ND — 04H ANE — 04H NH, seulement après la première passe; F — 04H NP et G — 04H N.
Fig. 2 :
Fig. 2 — Photomacrographies des pipes soudés en 304H. A — 04H NPB — 04H AC — 04H ND — 04H ANE — 04H NH
Fig. 3 :
Fig. 3 — Photomicrographies des passes de soudure sur 304H. A— 04H NPB — 04H AC — 04H ND — 04H ANE — 04H NH sousgrossissement 200 (attaque oxalique).
Des échantillons ont été préparés à partir des faces transverses et des racines de soudure , sur une longueur de 25 mm, puis soumis à essais avec un mandrin de 20 mm de diamètre et un angle de flexion de 180 degrés. De petits échantillons pour les essais de résilience ont été extraits de la coupe transversale, dans son épaisseur, avec l’entaille placée au centre du métal de lasoudure (WM), sur la zone affectée thermiquement ; 2 mm de l’interface de la soudure (FL+2mm) et sur le métal de base. L’essai de résistance aux chocs a été mené à 20°C, à -20°C, -40°C et -60°C.
Coupes transverses des soudures
Des photographies représentatives de la racine des soudures, montrant les couches d’oxydes de chrome (coloration à chaud) des pipes en 304H soudés sont présentées en Fig.1.
Les pipes en 304H, d’épaisseur 6 mm, ont été soudés avec six passes au total. En fonction de l’énergie totale (chaleur) appliquée, le matériau montre une large gamme de colorations, surtout les soudures effectuées sans inertage .
La Figure 1A-E montre les racines des soudures après la première passe suivie des cinq passes de finition.
Pour donner un meilleur aperçu et faire la corrélation avec la norme AWS D18.1 (Réf. 12), on montre aussi des photographies des racines après la seule première passe pour la soudure sans inertage (Fig 1F), et pour la soudure inertée à l’azote (Fig. 1G).
L’information donnée par la coloration après la première passe est moins nette qu’une fois la première passe et les cinq passes de finition effectuées (Fig 1A-G).
Cependant, on distingue parfaitement les différences entre les soudures en absence d’inertage et avec inertage , grâce à la largeur des zones colorées.
Les soudures avec inertage sont bien plus propres et avec des couleurs plus brillantes que la soudure sans inertage .
Le joint sans inertage aucun (04H NP) montre une couche d’oxyde de chrome très large (Fig 1A, F). Cette couche d’oxyde colorée affecte la résistance à la corrosion , puisqu’elle contient du chrome extrait du métal situé juste en dessous.
Néanmoins, pour les joints réalisés sous inertage : 04H A (Fig. 1B), 04H N (Fig. 1C, G), 04H
AN (Fig. 1D), 04H NH (Fig. 1E), la largeur de la zone colorée est plus faible, et sa couleur est moins intense que pour le joint non inerté, 04H NP. En particulier, sur le joint inerté avec un gaz contenant de l’hydrogène (04H NH), l’effet décolorant de H2 est parfaitement visible.
La Figure 2 montre les photomacrographies des soudures. Les différences de forme des racines, entre la soudure sans inertage(04H NP) et les autres soudures se voient parfaitement. La racine de la soudure 04H NP nécessite un nettoyage et une opération de remise en forme, ce qui induit des coûts supplémentaires par rapport aux autres joints dont la racine a une meilleure forme.
Les propriétés mécaniques des soudures sont affectées de manière significative par leur forme et leur composition. En ce qui concerne notamment la racine, un renforcement positif combiné à une transition douce entre la soudure et le métal de base sont nécessaires pour assurer une résistance mécanique optimale de la soudure .
Lors d’une soudure à l’arc, un paramètre important est le gaz d’inertage mis en œuvre, car il peut avoir une influence sur la forme, sur le mode de transfert du métal, et sur la distribution de l’énergie dans l’arc. Par exemple, la conductivité thermique de l’argon est très faible, ce qui affecte à la fois la forme de l’arc et celle de la soudure . Du coup, on obtient une soudure en forme de verre à vin.
Par contre, grâce à sa haute conductivité thermique , l’hydrogène permet d’avoir un arc plus étroit, dans lequel la concentration en énergie est supérieure, ce qui amène plus de pénétration.
L’hydrogène, un gaz réducteur, empêche la formation d’oxydes à la surface de la soudure . Du coup, la soudure est beaucoup plus belle. Cependant, H2 est très soluble dans les aciers, ce qui peut entraîner des porosités et de la fissuration, surtout dans les soudures d’aciers inox duplex (Réf. 4,13).
Tableau 2 —Composition chimique du métal d’apport utilisé lors de cette étude Composition (en poids-%) / Métal d’apport
Fig. 4 :
Fig. 4 — Photomicrographies de passes de soudure sur acier inox 304H.A — 04H NPB —04H AC — 04H ND — 04H ANE — 04H NHavec un grossissement 200, (attaque Lichtenegger).
Microstructure
La microstructure, pour tous les échantillons, était austénitique, avec un peu de ferrite, y compris dans les racines et les passes ultérieures, quel que soit le gaz d’inertage—Fig. 3. La coloration au réactif de Lichtenegger montre que le métal des soudures s’est solidifié essentiellement sous forme de ferrite—Fig. 4.
Tableau 3 :
Taux de ferrite
La composition chimique et l’historique thermique jouent sur le taux de ferrite dans les soudures d’aciers inox. Le taux de ferrite joue sur les propriétés de résilience , de résistance à la corrosion , sur la tenue à long-terme aux hautes températures, et, en particulier, sur la résistance à la fissuration à chaud (hot cracking).
C’est pourquoi il est important de s’assurer que le taux de ferrite reste dans les limites spécifiées. De façon générale, un taux de ferrite minimum de 3 est nécessaire pour assurer que la première phase à se solidifier est la ferrite, afin de procurer une bonne résistance contre la fissuration à chaud . Le diagramme WRC-92 peut être utilisé pour prédire le FN de la soudure avec une bonne approximation (Réf. 14) ; il donne aussi une idée sur le type de solidification que l’on peut attendre. Lorsqu’on compile les compositions du pipe et du métal d’apport, le diagramme indique que le taux de ferrite de la soudure sera d’environ 9.
Ajouter du N2 au gaz d’inertage (en protection de la racine) résulte clairement en un taux de ferrite plus faible dans la passe de racine. Le joint non inerté montre une valeur moyenne de 8, pour le taux de ferrite dans la passe de racine, alors qu’une valeur minimale de 1,5 a été obtenue sur la soudure inertée à l’azote.
Pour la soudure inertée à l’argon (04H A), une valeur moyenne de 4,3 a été obtenue, ce qui est assez bas comparé à la soudurenon inertée (04H NP). L’inertage avec N2+10% H2 (04H NH) montrait, lui, un taux moyen de 3,3. Ceci est important, et recherché en particulier pour des applications en raffineries, où la fissuration à chaud est un problème.
Le taux de ferrite prévu de 9 est en bon accord avec les valeurs mesurées sur la soudure non-inertée. La plupart des mesures et des valeurs prévues tombent bien dans la région F+A du diagramme qui prédit la solidification avec la ferrite en première phase. La ferrite en tant que première phase solidifiée est aussi confirmée par l’attaque avec le réactif coloré – Fig.4.
Fig. 5 — Photomicrographies du cordon envers montrant la corrosion intergranulaire des soudures.A — 04H NPB — 04H AC — 04H ND — 04H ANE — 04H NH.
Composition chimique
La composition chimique des bains racinaires a été déterminée par analyse chimique et figure dans le Tableau 5.
Les teneurs en N2, 02 et H2 (en ppm) des bains racinaires, déterminées par l’analyse chimique sur un Leco, sont détaillées dans le Tableau 6.
L’utilisation de N2 pur, de gaz riches en N2, de gaz N2+10%H2, comme gaz d’inertage, donne des valeurs constantes entre 820 et 7985 ppm dans les bains racinaires, alors que les valeurs étaient de seulement 485 et 445 ppm pour les bains sans inertageou avec inertage Ar, respectivement. Cela est en accord avec la teneur en ferrite, où le taux de ferrite (FN) descendait à 1,5 et 3,3 sous inertage à l’azote pur et sous azote avec 10% de H2.
Propriétés de dureté
Les valeurs de dureté Vickers pour les racines de soudure et le métal de base sont données dans le tableau 7. On n’a pas observé de différences de dureté significatives entre les racines de tous les joints.
Propriétés de résistance à la corrosion intergranulaire
En raison de la teneur en carbone relativement élevée du métal de base 304H par rapport à la nuance 304L, le risque decorrosion intergranulaire du 304H serait plus important que pour le 304L. C’est pourquoi, afin de mettre en évidence une éventuelle susceptibilité à la corrosion intergranulaire , des essais selon les normes TS EN 3157 et EN ISO 3651-2 ont été menés par immersion des échantillons dans une solution de sulfate de cuivre dans de l’acide sulfurique à ébullition pendant 20h, suivie d’une flexion .
L’azote a été ajouté au gaz de protection et /ou au gaz d’inertage, surtout pour accroître la résistance à la corrosion par piqûre , mais aussi pour améliorer la résistance mécanique , dans une certaine mesure.
La résistance à la corrosion du côté racine a aussi été accrue en utilisant du N2 pur ou du N2 additionné de 5 à 10% de H2, comme gaz d’inertage. De hautes teneurs en N2 et une exposition prolongée à de hautes températures finiraient par affecter les propriétés des soudures, puisque le N2 dans les aciers inox austénitiques joue un rôle semblable à celui du carbone , en accroissant la résistance mécanique , sans cependant les inconvénients liés à la précipitation de carbures et nitrures de carbone . Aucune défaillance n’a été détectée après flexion , ce qui est le signe d’une bonne résistance à la corrosion .
Le Tableau 5 montre des photomacrographies des échantillons utilisés pour l’essai de corrosion , y compris ceux du côté racine des joints.
Résistance à la corrosion par piqûre
L’essai de corrosion par piqûre a été mené selon l’ASTM G48. Les échantillons ont été immergés dans une solution de chlorure ferrique à 50°C pendant 72h. Les matériaux utilisés dans les industries pétrolières et gazières sont affectés de divers types decorrosion , souvent causés par l’eau de mer et des gouttelettes. En environnement marin, la corrosion par piqûre et la corrosioncaverneuse est fréquente, et, pour les nuances austénitiques, la fissuration par corrosion sous tension se produit aussi si le matériau est à une température supérieure à 60°C. De hautes températures, de hautes teneurs en chlorures, et des pH bas accroissent le risque d’attaques localisées dans tout environnement contenant des chlorures.
Le potentiel de corrosion électrochimique est aussi très important. Ce potentiel est affecté par l’activité biologique à la surface de l’acier. Dans la mesure où on peut considérer que l’eau de mer et les environnements associés sont des milieux vivants corrosifs, on a parfois du mal à définir quelles seront exactement les conditions en service. A des températures supérieures à 40°C, l’activité biologique va s’arrêter, et le potentiel corrosif va changer. Utiliser un ajout permanent de produits chlorés (chloration) pour stopper la prolifération de la vie marine peut accroître le potentiel corrosif. Normalement, la température critique decorrosion par piqûre (CPT, en anglais, pour « Critical Pitting Temperature ») est bien inférieure à 50°C pour la nuance 304H. Cependant, il faut garder à l’esprit que, lors d’applications en raffineries, là où des fluides très corrosifs circulent dans les tuyauteries, ces tuyauteries peuvent se dégrader en conditions de service. Ici, on a utilisé les durées et températures maximales pour l’essai, afin de simuler des conditions au-delà de l’extrême, pour obtenir rapidement des données permettant d’établir un classement (Réf. 15).
Les pertes de poids ont été mesurées, et sont présentées dans le Tableau 8. Les photomacrographies des échantillons ont été prises après l’essai de corrosion , et sont visibles sur la Fig.6. La plus faible perte de poids, indiquant la corrosion la plus faible, a été observée sur les échantillons inertés à l’argon. Les pertes de poids maximales semblent venir des soudures inertées avec du N2. Cependant, quand on examine les photographies, la plupart des piqûres sont visibles sur le métal de base et non dans le métal du joint .
Tableau 4 :
Tableau 4 — Taux de ferrite dans les soudures TIG de pipe en 304H Emplacement de la mesure Métal de base / Passe de racine, Welded joint code = Code du joint soudé , Cap pass = Passe terminale
Tableau 5 :
Résultats de l’essai de résistance à la rupture
Tous les échantillons ont parfaitement passé cet essai avec succès : la soudure a mieux résisté que le métal de base, qui a cassé en premier. La résistance à la rupture varie de 619 à 675 MPa (Tableau 9).
Résultats des essais de flexion
Aucun des échantillons de la racine ou de la soudure sur pipes en acier 304H n’a échoué au test de flexion .
Résultats des essais de résilience
Les résultats des essais de résilience des joints réalisés avec différents gaz d’inertage, et l’effet du gaz de protection , sont aussi montrés sous forme de graphe Fig. 7. Il n’y a pas de différences notables selon les différents gaz d’inertage, exception faite des joints réalisés sous inertage N2+10%H2.
Fig. 6 :
Fig. 6 — Photomicrographies montrant le côté racine des échantillons pour l’essai de corrosion par piqûre sur des soudures en 304H A — 04H NPB —04H AC — 04H ND — 04H ANE —04H NH.
Conclusions
Cette étude sur les effets du gaz d’inertage (protection de la racine) sur la microstructure, la résistance à la corrosion et les propriétés mécaniques de joints soudés TIG sur des pipes en 304H a conduit aux conclusions suivantes :
Les joints soudés sans aucun gaz d’inertage ont montré une large zone de dépôts d’oxydes de chrome (coloration), qui affectent la résistance à la corrosion . Sur les joints soudés sous inertage , la largeur de la zone colorée est plus faible, et la couleur est moins prononcée, par rapport aux soudures sans inertage . En particulier, sur les soudures inertées avec des gaz contenant de l’hydrogène, l’effet décolorant a été clairement observé.
L’emploi de gaz contenant de l’azote peut conduire à l’introduction de quantités significatives de N2 dans le bain en fusion , et cet effet est plus probable encore avec des racines de soudure plus larges et du soudage manuel. Cela a joué sur le taux de ferrite du métal dans la soudure , descendant jusqu’à 6 FN.
Pour les soudures effectuées sur un acier 304H avec du fil consommable en 308H, on ne devrait pas s’attendre à des problèmes de fissuration à chaud , puisque les soudures vont se solidifier avec une phase ferrite en premier. Cependant, il est recommandé de vérifier la composition de l’acier et du métal d’apport avec le diagramme WRC-92, afin de s’assurer qu’il y a une bonne marge de sécurité. Il est aussi judicieux de mesurer le taux de ferrite de la racine, si elle est accessible, puisque cela donne une indication pour savoir si le métal soudé s’est solidifié sous forme ferritique ou austénitique en premier. On doit cependant garder à l’esprit qu’une racine fortement chauffé à nouveau peut présenter un taux de ferrite inférieur à celui prédit dans le WRC-92, et que ce n’est pas nécessairement le signe d’un risque accru de fissuration à chaud .
On a observé une chute significative du taux de ferrite dans les bains racinaires quand on est passé de l’argon pur au mélange N2/H2 (90% N2+ 10% H2) ou à l’azote pur comme gaz de protection . Le taux de ferrite du cordon racinaire est descendu jusqu’à un FN de 6, par rapport aux soudures non inertées. Cependant, aucune tendance à la fissuration à chaud n’a pu être notée, et tous les cordons racinaires se sont solidifiés d’abord sous forme de ferrite, tel que prévu dans le diagramme WRC-92.
L’utilisation d’azote pur, ou d’azote additivé avec de l’hydrogène à 10 % comme gaz d’inertage a conduit à des valeurs identiques d’environ 820 et 795 ppm dans les bains racinaires, alors que des valeurs de seulement 485 et 445 ppm ont été relevées pour les soudures non inertées ou inertées à l’argon, respectivement. Ces données sont bien corrélées et en accord avec les données sur le taux de ferrite, là où le taux de ferrite est descendu à 1,5 et 3,3 dans l’azote pur et le mélange N2 90 %+ H2 10 % utilisés en inertage .
Les essais de corrosion par piqûre ont montré que ce type de corrosion était minimal sur les soudures inertées à l’argon, comparées aux soudures sans inertage . Les essais mécaniques n’ont pas mis en évidence de changement significatif en fonction du gaz d’inertage.
Les compositions de l’acier 304H et du métal d’apport 308H peuvent permettre d’employer des gaz riches en N2 pour la protection de la racine, sans risque notablement accru de fissuration à chaud . Cependant, il faut prendre en considération la teneur plus élevée en N2 lors du choix de l’acier et du métal d’apport. Il est recommandé de s’appuyer sur le diagramme WRC-92 pour vérifier l’existence d’une marge de sécurité suffisante par rapport aux compositions réelles, ainsi que de vérifier, si c’est possible, le taux de ferrite du cordon racinaire, afin d’éviter le risque de fissuration à chaud .
Tableau 6 — Analyse Leco des cordons racinaires soudés en TIG sur des pipes en 304H Code du joint soudé
Tableau 7 :
Tableau 7 — Dureté Vickers HV10 des soudures TIG sur pipes en acier 304H, sans et avec divers gaz d’inertage
Fig. 7:
Fig. 7 Résultats des essais de résilience sur des pipes en 304H soudés TIG
Tableau 8 :
Tableau 8 — Perte en poids après essai de corrosion par piqûre Code du joint soudé , Poids avant essai, Poids après 24h, Poids après 48h, Poids après 72h, Perte Totale
Tableau 9 :
Remerciement
Les auteurs souhaitent remercier l’aide financière et technique de Turkish Petroleum Refineries Co., Raffinerie d’Izmit dans le cadre du projet de R&D N° 2010/07. En outre, l’aide des collègues des Départements Inspection, R&D, et Chimie de la Raffinerie, et les contributions de Mehmet Bilgen, IWE, et de Asil Celik Corp. ont été très appréciables.
1. Bergquist, E. L., Huhtala, T., and Karlsson, L. 2011. The effect of purging gas on 308L TIG root pass ferrite content. Welding in the World 3/4, 55: 57–64.
2. Saggau, R. 2005. Investigation of the effect of yellow heat tints on the pitting corrosion behavior of welded stainless steels. PhD thesis, Technical University Carolo Wilhelmina at Braunschweig.
3. Ödegard, L., and Fager, S. A. 1993. The pitting resistance of stainless steel welds. Australasian Welding Journal, Second quarter, 24–26.
4. Fletcher, M. 2006. Gas purging optimizes root welds. Welding Journal 85(12): 38–40.
5. Sewell, R. A. 1997. Gas purging for pipe welding. Welding and Metal Fabrication.
6. Andersen, N. E. Welding stainless pipes, key technology for process industry applications. Svetsaren 1/2; 53–56.
7. Petersens, A. F., and Runnerstam, O. 1993. Selecting shielding gases for welding of stainless steels. Svetsaren 47: 2; 11–15.
8. Cuhel, J., and Benson, D. 2012. Maintaining corrosion resistance when welding stainless tube and pipe. Welding Journal91(11): 47–50.
9. Li, L. J., and Davis, T. 2007. Effect of purging gas oxygen levels on surface structure and mechanical properties of GTA welded Type 304 stainless sanitary tube. Journal of Advanced Materials 39(4): 14–19.
10. McMaster, J. 2008. Using inert gases for weld purging. Welding Journal 87(5): 40–44.
11. Gooch, T. G. 2010. Welding new stainless steels for the oil and gas industry. The Welding Institute, March, 16 pages.
12. D18.1/D18.1M:2009, Specification for Welding of Austenitic Stainless Steel Tube and Pipe Systems in Sanitary (Hygienic) Applications. American Welding Society, Miami, Fla.
13. Tusek, J., and Suban, M. 2000. Experimental research of the effect of hydrogen in argon as a shielding gas in arc welding of high alloy stainless steel. Int’l Journal of Hydrogen Energy 25: 369–376.
14. Lippold, J. C., and Kotecki, D. J. 2005. Welding Metallurgy and Weldability of Stainless Steels. John Wiley & Sons, New Jersey.
15 MIG welding stainless steel gas mixes. www.weldreality.com/stainlesswelddata.htm. Visited on May 19, 2010.
Traduction de “Effect of the Purging Gas on Properties of 304H GTA Welds” paru dans Welding Journal en avril 2014. Traduction Partick Dubosc et Clémence RETEL en mai 2015. Autorisation des auteurs reçue.